Production measurements and recording
Production recording benefits from several measurements, many of which are used in a complementary capacity to determine fluid and flow properties. Fluid velocity is usually measured with a rotary flow meter – a blade that rotates when fluid passes near it. Under ideal conditions, the blade rotation speed in revolutions per second (RPS) is proportional to the fluid velocity. Friction on roller bearings and effects from fluid viscosity result in nonlinear velocity responses, which require calibration of the measurement. This calibration is performed by making transitions up and down with different cutting speeds. Before calculating the absolute velocity of the fluid, the speed of the roller is corrected for the relative velocity of the vehicle. Due to friction near the tube wall, the absolute velocity of the fluid is not the same as the average velocity of the fluid moving through the tube. After applying corrective factors, engineers convert the rotational speed to an average speed using computer modeling techniques, which present the fluid velocity profile along the diameter of the tube.
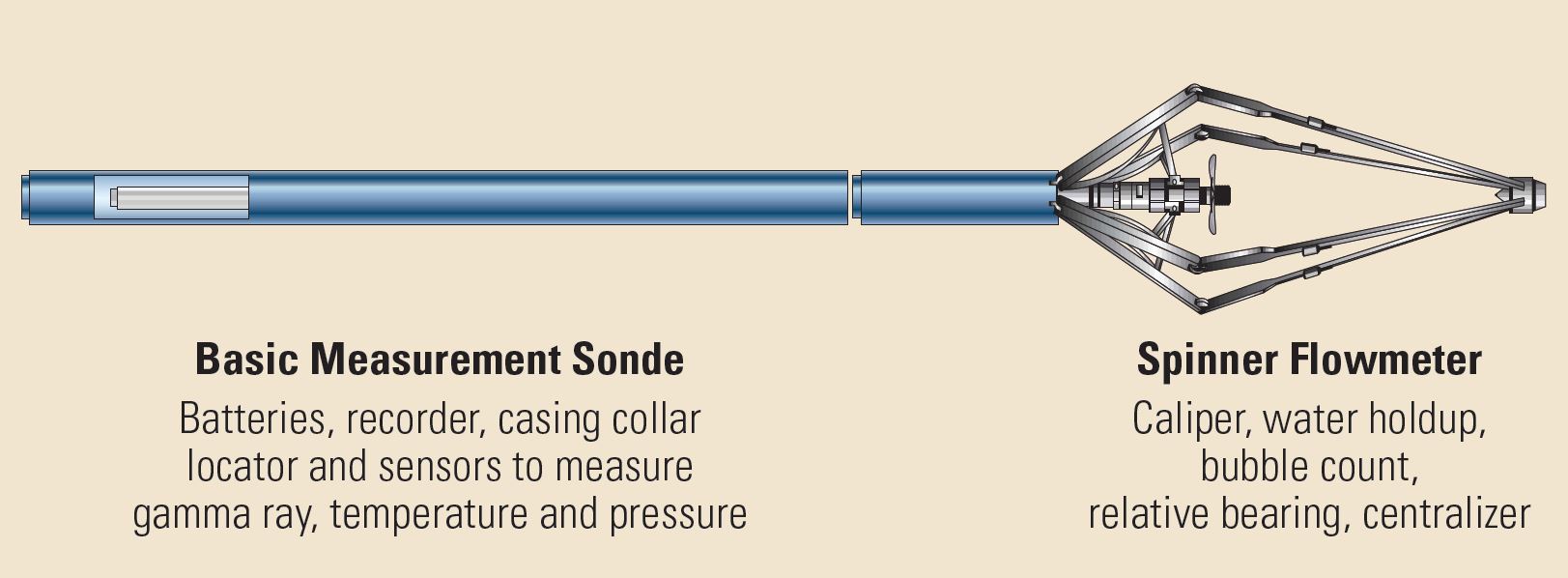
For reservoir and production engineers, pressure is a comprehensive measurement with several applications. Strain gauges, sapphire and quartz are the main devices used to measure pressure. Engineers can also measure pressure using a manometer – a device that converts mechanical displacement into pressure. From well pressure data, engineers can determine well stability at the time of cutting, estimate reservoir pressure from multi-scale cutting studies, calculate fluid density, and obtain key reservoir parameters by performing velocity analyzes. transient.
Temperature is an integral measurement for all output cuts. Engineers use temperature data to make qualitative conclusions about fluid inputs, especially in low-velocity flow scenarios in which a rotator may not be sensitive enough to detect motion. Gas inlets create cooling anomalies that are easily detected using temperature registers. Temperature measurements are also used in the evaluation of fracture treatment and to evaluate the performance of the injection well. Using temperature data, engineers may be able to assess the integrity of well ends, detect cage leaks, and identify flow through channels behind the pipe. Resistance temperature detectors (as the most common type of sensor), usually consist of a platinum wire or film deposited on a non-conductive surface. Changes in temperature cause changes in resistance, which is calibrated and converted to temperature.
Liquid density measurements identify oil, gas, and water. Service companies have developed tools on a set of physical principles to provide fluid density measurements:
- Differential pressure at two ports separated by a known distance
- "Compton" distribution of gamma rays
- Pressure gradient with respect to density
- Flow vibration in relation to density and viscosity.
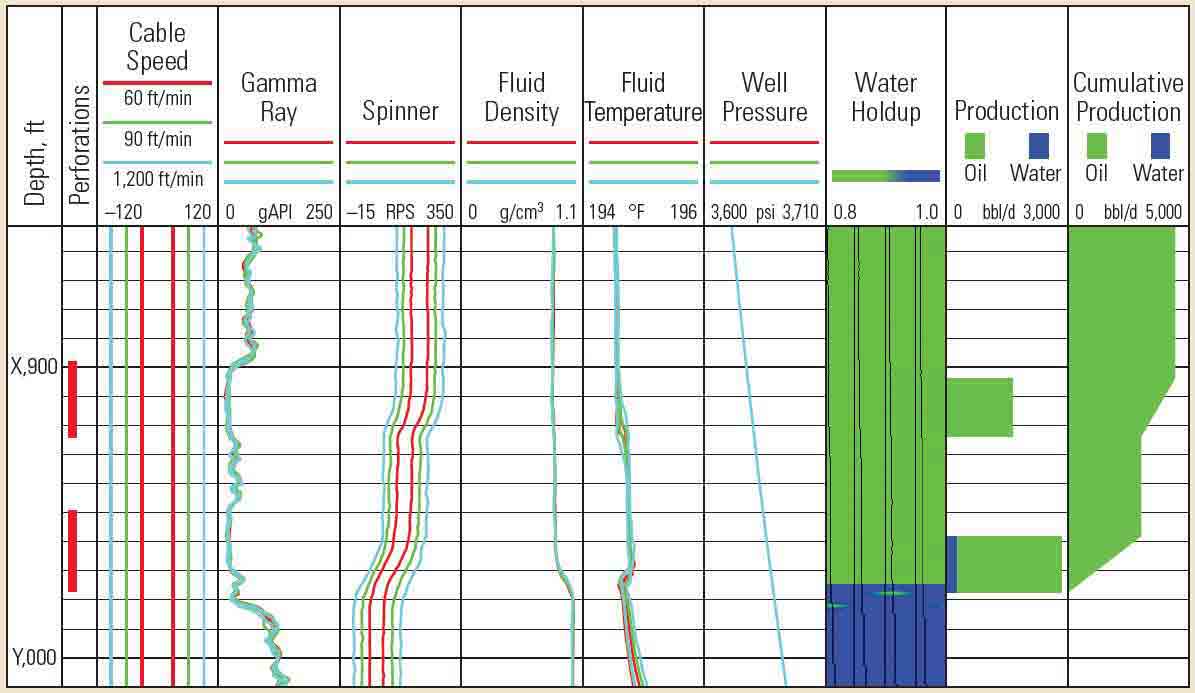
In the case of two-phase flow, engineers can use fluid density – in conjunction with other measurements (such as fluid viscosity) – to calculate retention. When multiphase leakage is present, they should use tools with probes dispersed through a well, to directly measure fluid retention. A device senses differences in optical reflection to understand holding, which involves measuring the amount of light reflected by a liquid. Another device distinguishes water from oil and gas using probes that measure the electrical properties of liquids.
Auxiliary measurements, provided mainly by output cutting ranges, are the outer layer “collar” trunks, gamma ray, caliper and deflection data. The “collar” layer and gamma ray data provide depth control and correlation with the finishing components. Caliper and deviation data are used in production modeling programs.
Production logs can be difficult to interpret because fluid flow may not be uniform and multiple transitions result in large amounts of data, some of which may produce contradictory responses. Computer programs have been developed to assist engineers in understanding pit conditions. Computer-generated interpretations remove some of the ambiguities associated with the interpretation process (below). The interpretation product can often help the engineer identify more productive intervals, detect water ingress, and determine intervals that do not contribute to production.
Power modes
To analyze output cut-off data, production engineers need to be aware of downstream regimes. Knowing the expected current regimes allows operators to select measurements suitable for the pit conditions.
Single-phase current – when only oil, gas or water is produced – flow is easier to estimate. However, this is unusual in most wells.
Two- and three-phase flows – involving mixtures of two or three types of liquids – can exhibit a wide variety of current regimes and are complicated by diversion wells (right). In such cases, gravity ensures that the lighter phase operates at a greater speed than the denser phases. The speed difference between different fluids is considered to be the sliding speed.
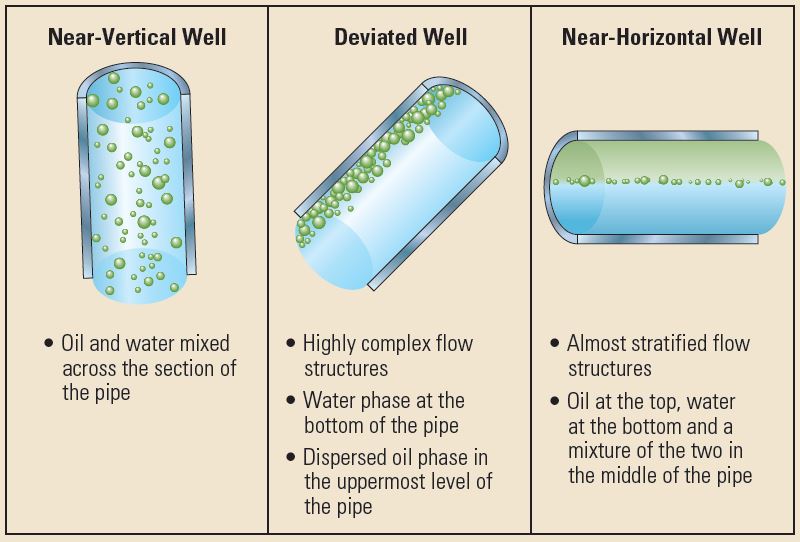
Ndërsa lëngjet migrojnë lart, regjimi i rrymës zakonisht ndryshon. Për shembull, nafta me gaz të tretur mund të hyjë në pus si një fazë e vetme. Presioni hidrostatik zvogëlohet ndërsa vaji ngrihet dhe flluskat e gazit fillojnë të formohen në vaj. Regjimi i rrymës kthehet më pas në rrymë flluskash. Presioni zvogëlohet më tej ndërsa përzierja lëviz lart; formohen më shumë flluska dhe flluska më të vogla grumbullohen për të krijuar flluska më të mëdha. Flluskat e mëdha, ose gazrat, udhëtojnë më shpejt se sa flluskat e vogla dhe lëngjet. Gjurmët e gazit mund të iniciojnë rrjedhjen e slugut. Slugu priret të bashkohet me të ngjashmin dhe të lëvizë në qendër të tubit, duke orientuar pjesën më të madhe të vajit të rrjedhë përgjatë mureve të tubit. Ky regjim rryme quhet rrymë shkume. Përfundimisht, mund të arrihet një regjim i rrymës së mjegullës, në të cilin gazi bart pika vaji dhe të dy lëngjet po udhëtojnë në thelb me të njëjtën shpejtësi. Ky shembull i thjeshtuar bëhet kompleks në puset e devijuara ose kur lëngjet e fazave të ndryshme hyjnë në pus nga zona të shumta. Programet e modelimit përpiqen të zgjidhin këto kompleksitete duke përdorur të dhënat e regjistrit të prodhimit.
Supervision and management of reservoirs
Production logs help engineers diagnose problems that occur during the life of a single well. They are also used for the management and supervision of multiple wells or the entire reservoir. A common challenge faced by operators is identifying areas that produce excess water. The water produced affects the surface treatment operations because the water must be separated from the flow stream to be disposed of. The water produced can also affect the performance of the well by limiting the volume of hydrocarbons produced. After identifying water production areas, relevant engineers can make repairs to reduce or eliminate water production.
Operators can also use production logs to calibrate reservoir simulation models. When matching reservoir model history, engineers can use production log data to help identify or match zonal contributions, accurate parameters, and align model with empirical performance data.
Lifetime registration
Production logs help engineers diagnose problems that occur during the life of a single well. They are also used for the management and supervision of multiple wells or the entire reservoir. A common challenge faced by operators is identifying areas that produce excess water. The water produced affects the surface treatment operations because the water must be separated from the flow stream to be disposed of. The water produced can also affect the performance of the well by limiting the volume of hydrocarbons produced. After identifying water production areas, relevant engineers can make repairs to reduce or eliminate water production.